How Are Tilt-Up Walls Constructed?
- erica6918
- Jan 27, 2023
- 3 min read
Updated: Aug 9, 2024
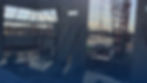
Large precast concrete panels are tilted into place during the construction of commercial buildings using the tilt-up technique. It has been used since the early 1900s. These panels, also known as "tilt-up panels" or "tilt-wall panels," are common in many commercial structures. The Tilt-Up method is known for its efficiency, speed, and cost-effectiveness.
How Are Tilt Walls Made?
The forms for tilt-up construction are custom-made to match the final design of the building, with rebar cut to the appropriate size. Once the concrete is poured and cured, the precast panels are tilted into place to form the exterior walls of the building.
How Are Tilt-Up Walls Constructed?
With tilt-up construction, walls are built horizontally using wooden forms, rebar, and concrete that has been poured. The concrete is poured into custom-made forms to create reinforced slabs that will later be tilted into place as the walls of a building.
How Are Tilt-Up Walls Connected?
In Tilt-Up construction, the wall slabs are connected by inserting bent dowel bars or threaded inserts into the panel during concrete curing. The bars, or inserts, that secure the connection between the slabs are cast into the panel. Alternatively, dowel bars can be set into precast panels.
What Is the Difference Between Tilt-Up and Precast Walls?
In tilt-up construction, concrete panels are poured and cast on the building site and then lifted into position. Precast concrete, on the other hand, is made somewhere else, then transported to the construction site where it is needed.
How Do Tilt-Up Walls Compare to Other Walls?
Tilt-up construction has become one of the construction methods of choice due to its cost-effectiveness as the size of a building increases. The ability to quickly erect panels that protect the building, the people inside, the equipment, and the supplies from inclement weather also enables quicker construction of structures.
Tilt-up projects also give contractors more control because they are typically put together on-site using labor and materials that are close by, as opposed to other construction techniques that call for specialized materials or skilled labor that have longer lead times and higher costs.
What Are the Advantages of Tilt-Up Walls?
Tilt-up walls offer various advantages that can lower project expenses, shorten the construction schedule, and increase the value of commercial buildings.
Speed Tilt-Up construction is fast, with concrete panels cured in a few days and the tilting process being quicker and less labor-intensive. Additionally, later stages of the construction like roof and infrastructure integration can start earlier as Tilt-Up encloses the building sooner.
Labor costs and materials Tilt-Up requires less skilled labor than other methods, only needing laborers to pour and finish the concrete walls and a crane operator to lift them into place. Also, construction materials such as ready-mix concrete and rebar are readily available from local suppliers, without the need to wait for months for steel beams or complex components.
Energy efficiency Reinforced concrete is a good insulator and its thermal properties can be improved by adding extra insulation layers for energy savings. Though it may result in higher costs initially, Tilt-Up concrete panels can cut energy costs over time.
Contact Reliable Commercial Construction to Start Your Commercial Project
Want to see whether Tilt-Up walls are the answer for your next commercial project? Contact Reliable Commercial Construction. We have been in business for over 35 years and know all the tried and true methods of creating cutting-edge buildings.